You don’t have to know everything there is to know about high power laser welding. You’ve got us.
Posted on December 17, 2019 in Blogs
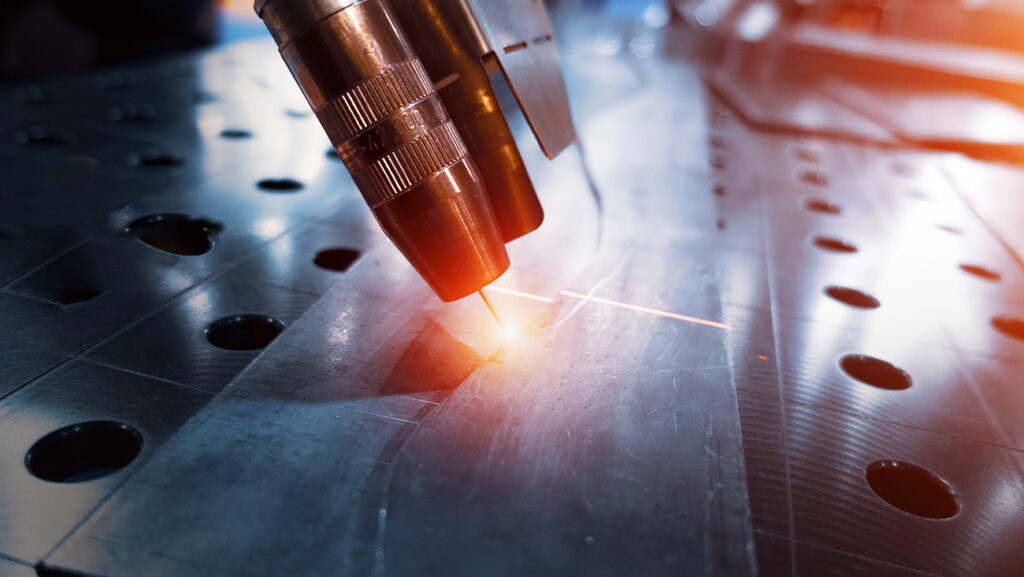
If you’re a fan of good TV commercials you’ve probably been enjoying AT&T’s most recent campaign “Just OK is not OK”. As a product designer, researcher, engineer, product manager, or production manager, you can surely relate. Perhaps you’ve received a response back from less experienced laser job shops like: “Just send us your specs. We’ll figure it out.” It’s responses like this that send you researching on your own to figure out best approaches, metal properties, and so forth, only to have wasted a whole lot of time that you could have been focusing on something else.
In our experience, even some of the smartest engineers we know still struggle with the incredible amount of material science and metallurgy knowledge required to make the most informed decision for any laser weld. So, you might say, that for you, just an OK amount of knowledge is just fine. Or you might find that you need a laser welding service partner who is willing to listen, do a deep dive into your application, and help you make the most informed process or material decisions you can. And to get you a leg up today, here are a few of the most common laser welding questions and answers. Consider them lesson #1.
What is the best base and filler material selection for my application?
Accumet uses fiber laser welders whereby NO filler material is required. Traditional welding methods require filler material to enable dissimilar metal welding. This technique can lead to the production of joint-weakening intermetallics and present an expensive and complex process. With Accumet’s fiber laser welding offering, the interaction of materials and the laser beam eliminates the need for filler materials and enables many new options for dissimilar metal welding.
If there’s no filler material, does that mean all metals can be welded together?
A major challenge with most other welding methods is the joining of dissimilar metals, and even two pieces of some metals such as aluminum and new alloys are not compatible to weld to each other. Our engineering staff is available to assist you with material selection choices, ensuring compatible, weldable materials are part of your design.
What is the most likely thing that will impact joint resistance, corrosion and fatigue life?
There are a few factors that will impact a quality weld. High up on the list is cleanliness. The welded area must be clean, free of oils and other contaminants, otherwise, there will be a negative impact on the weld. Another factor is simply a poorly executed weld. When joining materials together, it’s important to consult with our technical experts to zero in on the best place to weld to minimize the risk of cracking, corrosion, and/or weld defects that could lead to time-consuming and costly rework.
Can you comply with my laser welding specifications?
Adhering to our customers’ requirements and our quality compliant standards is a must. Our engineers and technicians have years of certified welding experience and advanced skills. Plus, our internal process specifications and quality controls meet the strictest standards in accordance with our ISO9100:2015 and AS9100:2016 certifications.
Can you integrate your laser welding services with our manufacturing steps?
Yes, our laser welding services are highly automated for customers who require high volume and consistent repeatability. Our laser welding is used extensively in the medical, electronics, and aerospace industries, among others, to achieve the highest quality welds for economical, high-volume applications and mission-critical secondary manufacturing.
Can you weld plastic?
Plastic welding is becoming extremely useful in medical and aerospace applications requiring highly consistent and reliable structures that are lightweight and chemically/environmentally resistant. There are specific plastics that lend themselves well to fiber laser welding under specific circumstances. Please inquire for more details.
The team at Accumet has years of expertise and can help you address your toughest laser welding challenges. Our certified laser welding technicians can perform high speed laser welding services with high power and high-quality processing rates for very narrow and precise weld bead placements, and with much less workpiece distortion compared to traditional welding. Our highly skilled fiber laser welding team is able to perform highly complicated welds on small 3D geometries, and many other complex applications where other industrial welders won’t dare to go.
For additional information about laser welding, metallurgy, joint design, and fatigue strength considerations, visit our laser welding page or contact us. We keep up with the latest advances in materials engineering and advanced production techniques to enable our customers to innovate faster and outperform their competition. To request pricing for your next laser welding job, visit our Request a Quote page.